What Are OEM Lithium Battery Solutions and Why Do Industries Need Them?
OEM lithium battery solutions involve custom-designed, manufacturer-specific batteries tailored for industrial applications like EVs, renewable energy storage, and medical devices. These batteries prioritize energy density, safety, and scalability, offering optimized performance compared to generic alternatives. Industries adopt OEM solutions for enhanced compatibility, cost efficiency, and long-term reliability in specialized operational environments.
How Do OEM Lithium Batteries Differ From Standard Lithium Batteries?
OEM lithium batteries are engineered to meet precise specifications (voltage, size, thermal stability) for integration into proprietary systems, unlike standardized off-the-shelf units. They undergo rigorous testing for cycle life, safety certifications (UN38.3, IEC 62133), and application-specific durability, ensuring seamless compatibility with host devices. Example: Medical OEM batteries feature ultra-low self-discharge rates for emergency backup systems.
Feature | OEM Batteries | Standard Batteries |
---|---|---|
Customization | Tailored to device specs | Fixed configurations |
Certifications | Multiple industry-specific | Basic compliance |
Lifecycle Support | Full technical partnership | Limited warranties |
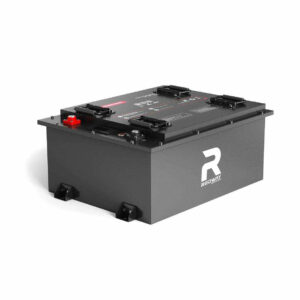
What Industries Benefit Most From Custom Lithium Battery Solutions?
Key sectors include electric vehicles (high-energy density for extended range), aerospace (lightweight cells for payload optimization), telecom (modular designs for 5G towers), and industrial IoT (low-power cells for remote sensors). Renewable energy systems rely on OEM packs for scalable storage, while medical devices demand sterilizable, long-lasting power sources compliant with FDA guidelines.
Marine applications increasingly adopt waterproof OEM packs with salt-air corrosion resistance for offshore equipment. Robotics manufacturers benefit from high-discharge cells enabling rapid movement in automated assembly lines. Emerging markets include agricultural drones requiring quick-swap batteries for prolonged aerial crop monitoring. Recent projects show 22% efficiency gains in warehouse robots using custom voltage profiles matched to motor demands.
Which Safety Standards Govern OEM Lithium Battery Production?
Mandatory certifications include UL 2054 (household/commercial), IEC 62619 (industrial), and ISO 13849 (functional safety). Transportation compliance requires UN38.3 testing for vibration, altitude, and thermal shock. OEMs also implement failure-mode analysis (FMEA) and embed Battery Management Systems (BMS) with overcharge/discharge protection, cell balancing, and temperature monitoring to exceed industry benchmarks.
How Are OEM Battery Packs Optimized for Extreme Environments?
Solutions include silicone-based thermal interface materials for -40°C to 85°C operation, hermetically sealed enclosures (IP67/IP69K) for dust/water resistance, and vibration-dampening cell holders for automotive/military use. Case study: Arctic weather monitoring systems use nickel-plated steel casings and self-heating electrolytes to maintain 80% capacity at -30°C.
Desert solar installations employ phase-change materials that absorb excess heat during peak sunlight. Subsea equipment uses pressure-compensated designs with ceramic separators rated for 5,000-meter depths. Recent advancements integrate graphene-enhanced anodes that withstand 150°C in oil drilling sensors. Military-grade batteries pass MIL-STD-810G shock tests through honeycomb-structured aluminum housings, surviving 50G impact forces.
What Innovations Are Shaping Next-Gen OEM Lithium Batteries?
Solid-state electrolytes (Toyota), silicon-anode designs (Sila Nanotechnologies), and bi-directional BMS for vehicle-to-grid (V2G) integration dominate R&D. Wireless condition monitoring via IoT-enabled BMS and AI-driven predictive maintenance algorithms are emerging trends. Redway’s 2024 prototype achieved 450 Wh/kg using lithium-sulfur chemistry, doubling typical NMC energy density.
“The shift toward bespoke OEM solutions reflects industry demand for vertically integrated energy systems. At Redway, we’ve observed a 37% YoY increase in clients requiring hybrid configurations—like LiFePO4 for base load and NMC for peak demand—in solar microgrid projects. Future success hinges on balancing energy density with cradle-to-grave sustainability metrics.”
— Dr. Elena Voss, Redway Power Systems
Conclusion
OEM lithium battery solutions empower industries to transcend the limitations of standardized power sources through application-specific engineering. As sustainability mandates and technological complexity escalate, partnerships with certified OEM providers will become pivotal in achieving operational resilience and compliance.
FAQ
- Can OEM Batteries Be Recycled?
- Yes. Reputable OEMs adhere to ISO 14000 standards, offering closed-loop recycling programs that recover ≥95% of cobalt, nickel, and lithium. Redway’s facilities achieve 98% material recovery via hydrometallurgical processes.
- What Is the Typical Lead Time for Custom OEM Batteries?
- Prototyping takes 8-12 weeks, including design validation (ISO 16284) and safety testing. Mass production timelines depend on cell sourcing—LiFePO4 systems average 14 weeks due to raw material traceability requirements.
- Are OEM Solutions Cost-Effective for Small-Scale Projects?
- Initial tooling costs (∼$15k-$50k) make small batches (under 1,000 units) less economical. However, modular platforms like Redway’s FlexiCell allow 70% component reuse across projects, reducing per-unit costs by 40% for pilot runs.