What Are the Best Lithium Battery Solutions for AGVs and Electric Vehicles?
Lithium batteries power AGVs (Automated Guided Vehicles) and electric vehicles (EVs) with high energy density, fast charging, and long lifespan. Lithium-ion (Li-ion) and lithium iron phosphate (LiFePO4) are popular choices for their efficiency and safety. These batteries support automation, reduce downtime, and meet sustainability goals. Choosing the right solution depends on application needs, cost, and environmental factors.
How Do AGVs and Electric Vehicles Benefit from Lithium Batteries?
AGVs and EVs use lithium batteries for higher energy efficiency, lighter weight, and longer operational cycles. These batteries enable fast charging, reducing downtime in industrial settings. For EVs, lithium solutions enhance driving range and performance. AGVs benefit from precise power management, enabling 24/7 automation. Both applications rely on lithium tech for sustainability and cost-effectiveness.
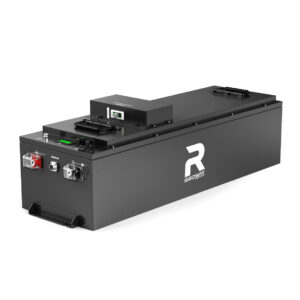
What Types of Lithium Batteries Are Used in AGVs and EVs?
Li-ion (NMC, LCO) and LiFePO4 are common. NMC offers high energy density for EVs, while LiFePO4 provides thermal stability for AGVs. Solid-state lithium batteries (emerging) promise safer, longer-lasting performance. Each type balances energy output, safety, and lifecycle. AGVs often use LiFePO4 for durability, while EVs prefer NMC for compact energy storage.
NMC (Nickel Manganese Cobalt) batteries are favored in EVs due to their ability to store more energy per unit weight, which directly translates to longer driving ranges. However, they require robust thermal management systems to mitigate overheating risks. LiFePO4 (Lithium Iron Phosphate) batteries, on the other hand, excel in industrial applications like AGVs because of their inherent stability and resistance to thermal runaway, even under frequent charge-discharge cycles. Emerging solid-state lithium batteries replace liquid electrolytes with solid alternatives, reducing flammability and enabling higher energy densities. These are particularly promising for heavy-duty EVs and AGVs operating in high-temperature environments.
Battery Type | Energy Density | Cycle Life | Common Use |
---|---|---|---|
NMC | High | 1,000-2,000 cycles | Electric Vehicles |
LiFePO4 | Moderate | 3,000-5,000 cycles | AGVs |
Solid-State | Very High | 5,000+ cycles | Future EVs/AGVs |
What Are the Key Challenges in Lithium Battery Adoption?
High upfront costs, thermal management, and recycling complexities hinder adoption. AGVs require batteries that withstand constant charging cycles, while EVs need affordable, high-capacity units. Safety risks like thermal runaway demand advanced BMS (Battery Management Systems). Supply chain shortages for lithium/cobalt also delay scalability.
How Does Battery Management System (BMS) Optimize Performance?
BMS monitors voltage, temperature, and charge cycles to prevent overcharging/overheating. For AGVs, it ensures stable power during repetitive tasks. In EVs, BMS maximizes range and battery lifespan. Advanced BMS uses AI to predict failures and optimize energy distribution, critical for safety and efficiency in both applications.
What Future Trends Will Shape Lithium Battery Technology?
Solid-state batteries, silicon-anode tech, and sodium-ion alternatives aim to replace traditional lithium. Wireless charging for AGVs and ultra-fast EV charging (10-minute full charge) are emerging. Recycling innovations will address sustainability. AI-driven BMS and modular designs will dominate next-gen solutions.
What Safety Standards Govern Lithium Batteries in AGVs/EVs?
UN 38.3 (transport), IEC 62133 (safety), and UL 2580 (EVs) certify lithium batteries. AGV batteries require ISO 13849 for operational safety. Thermal management, crash-testing, and fail-safe BMS are mandated. Compliance ensures fire/explosion prevention and stable performance in extreme conditions.
How Do Recycling Processes Impact Sustainability?
Hydrometallurgical recycling recovers 95% lithium/cobalt, reducing mining needs. AGV/EV manufacturers partner with recyclers like Redwood Materials for closed-loop systems. EU regulations mandate 70% battery recycling by 2030. Sustainable disposal lowers carbon footprint and cuts production costs by reusing materials.
Recycling lithium batteries involves two primary methods: hydrometallurgical and pyrometallurgical processes. Hydrometallurgy uses chemical solutions to extract metals like lithium, cobalt, and nickel, achieving recovery rates above 90%. Pyrometallurgy, which involves smelting at high temperatures, is less efficient but handles larger volumes. Companies like Redwood Materials are pioneering closed-loop systems where materials from end-of-life EV batteries are directly reused in new AGV or EV batteries. However, challenges persist, such as the high energy consumption of recycling plants and the logistical complexity of collecting spent batteries. Regulatory frameworks, such as the EU’s Battery Directive, are pushing manufacturers to design batteries with disassembly and recycling in mind, fostering a circular economy.
Recycling Method | Material Recovery Rate | Energy Consumption |
---|---|---|
Hydrometallurgical | 90-95% | Moderate |
Pyrometallurgical | 70-85% | High |
What Cost Factors Influence Lithium Battery Deployment?
Raw material prices (lithium, cobalt) account for 40-50% of costs. AGV batteries need higher cycle life, raising production expenses. EVs require large-scale, low-cost manufacturing. Recycling and cheaper alternatives (sodium-ion) will reduce prices. Government subsidies and economies of scale also drive affordability.
Expert Views
“AGVs demand batteries that balance energy density and cycle life. LiFePO4 is ideal for its stability in high-usage environments,” says a Redway Battery engineer. “For EVs, advancing solid-state tech will revolutionize range and safety. The industry must prioritize recycling infrastructure to meet 2030 sustainability targets. Collaborating with tech firms to integrate AI into BMS is critical.”
Conclusion
Lithium batteries are pivotal for AGVs and EVs, offering unmatched efficiency and adaptability. Challenges like cost and safety are being mitigated through innovations like solid-state tech and AI-driven BMS. Sustainable practices and regulatory compliance will shape the future, making lithium solutions the cornerstone of electric mobility and industrial automation.
FAQs
- How Long Do Lithium Batteries Last in AGVs?
- AGV lithium batteries last 2,000-5,000 cycles (5-8 years) with proper BMS. Usage intensity and charging patterns affect lifespan.
- Can EV Batteries Be Repurposed for AGVs?
- Yes. Retired EV batteries with 70-80% capacity can power AGVs. This reduces costs and supports circular economy goals.
- Are Lithium Batteries Safe in High-Temperature Environments?
- LiFePO4 batteries operate safely up to 60°C. Advanced BMS and cooling systems prevent thermal runaway in extreme conditions.