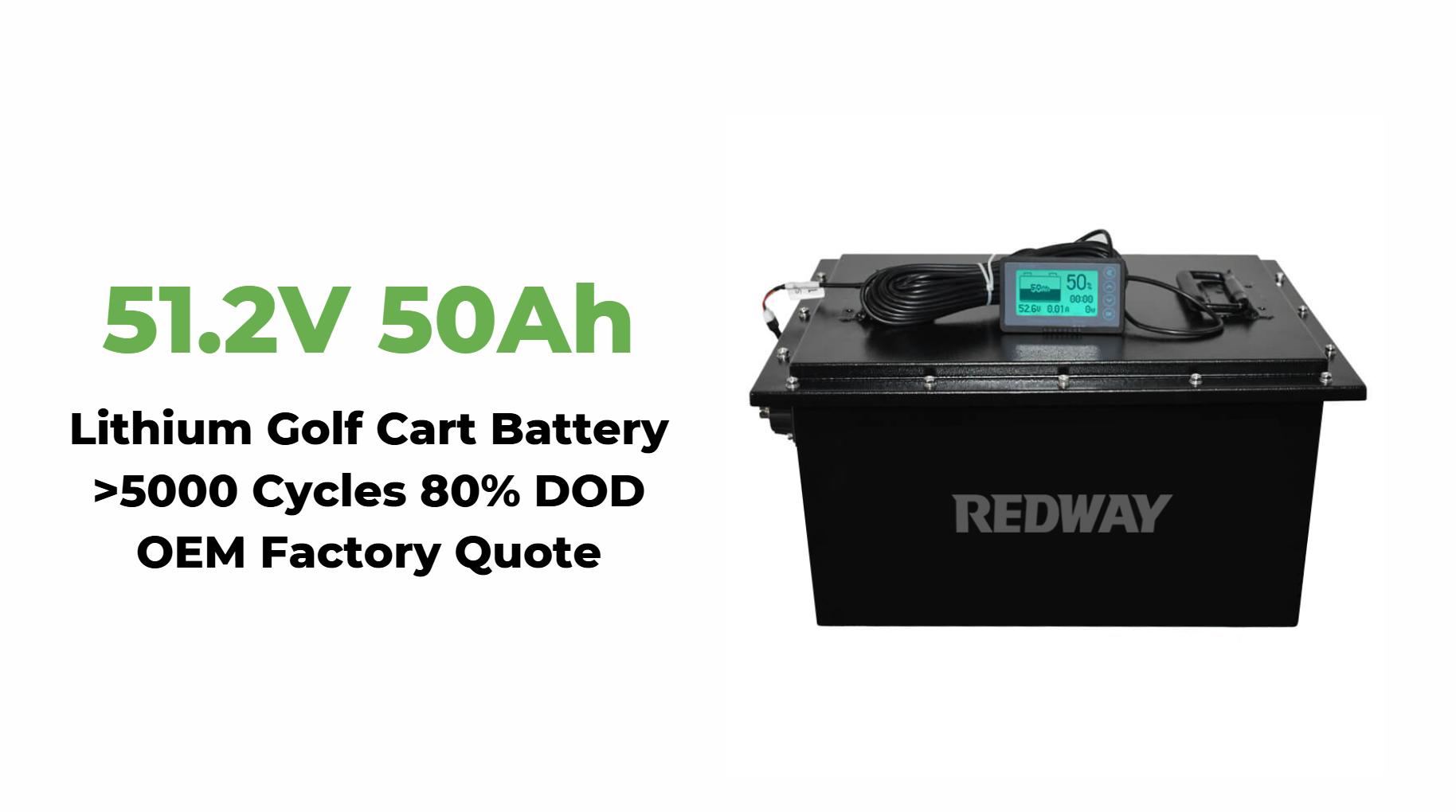
What Happens if a LiFePO4 Battery Gets Wet? Risks, Reactions, and Recovery
If a LiFePO4 battery gets wet, the outcome depends on its design and exposure level. Brief splashes or high humidity may have minimal effect if the battery is well-sealed, but submersion or prolonged water contact can cause corrosion, short circuits, and even hazardous reactions. Water can compromise safety, performance, and lifespan-so Fasta Power recommends keeping all LiFePO4 batteries dry and protected.
How does water exposure affect LiFePO4 batteries?
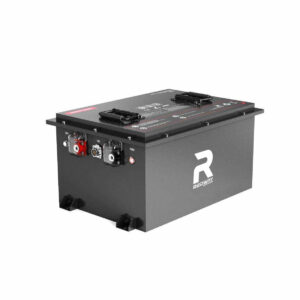
Water exposure can damage the internal components of a LiFePO4 battery, even though these batteries are more stable than other lithium chemistries. Moisture can cause corrosion of metal parts, disrupt the electrolyte, and create unintended electrical pathways. This may result in short circuits, reduced performance, or even complete battery failure. Fasta Power emphasizes that while some batteries have water-resistant casings, direct contact with water should always be avoided.
Chart: Effects of Water on LiFePO4 Batteries
Exposure Type | Immediate Risk | Long-Term Risk |
---|---|---|
Splash/High Humidity | Minimal if sealed | Potential corrosion |
Submersion | Short circuit, damage | Irreversible failure |
Saltwater | Rapid corrosion | Accelerated degradation |
What are the immediate dangers if a LiFePO4 battery gets wet?
The most immediate danger is the risk of a short circuit. Water can bridge the battery terminals or seep into the casing, creating a conductive path and causing uncontrolled current flow. This can lead to sudden power loss, overheating, or even fire. Fasta Power warns that if the battery is damaged or improperly sealed, the risk escalates quickly, especially in saltwater environments.
Why does corrosion occur in wet LiFePO4 batteries?
Corrosion occurs because water reacts with the battery’s metallic components, especially if it penetrates the casing. In saltwater, the process accelerates as dissolved salts enhance conductivity and chemical reactions. Corrosion degrades contacts, terminals, and internal circuitry, leading to reduced efficiency, voltage drops, and eventual battery failure. Fasta Power’s engineering team stresses that corrosion is often irreversible and a leading cause of premature battery death after water exposure.
Which LiFePO4 batteries are designed to resist water exposure?
Some LiFePO4 batteries, like those used in marine or outdoor applications, are built with waterproof casings and high IP (Ingress Protection) ratings. For example, batteries rated IP67 or IP68 can withstand submersion for limited periods. Fasta Power and other leading brands offer custom waterproof solutions for harsh environments, but even these should not be intentionally submerged unless specified by the manufacturer.
How do you check if your LiFePO4 battery is water-resistant?
Check the battery’s datasheet or label for an IP rating. IP65 means protection against water jets; IP67 or IP68 indicates resistance to temporary or prolonged submersion. Fasta Power recommends regular inspection of seals and casings, especially if the battery is used in wet or humid environments. Any visible cracks or wear can compromise water resistance.
What should you do if your LiFePO4 battery gets wet?
Immediately disconnect the battery from any devices and power sources. Wipe off visible moisture with a dry cloth-never use heat sources like hair dryers. Allow the battery to dry in a cool, ventilated area. Inspect for signs of corrosion or damage. If the battery malfunctions or you notice swelling, leaking, or odd smells, contact Fasta Power or a battery professional for guidance.
Chart: Emergency Steps if LiFePO4 Battery Gets Wet
Step | Action |
---|---|
Disconnect | Remove from devices and power sources |
Dry | Wipe with a dry cloth, air dry |
Inspect | Look for corrosion, swelling, leaks |
Consult | Contact Fasta Power or a professional |
Why is salt water especially dangerous for LiFePO4 batteries?
Salt water greatly increases the risk of corrosion and short circuits due to its high conductivity. It accelerates chemical reactions that degrade battery terminals, casing, and internal components. Fasta Power cautions that saltwater exposure can quickly render a battery unsafe or unusable, and such batteries should be professionally inspected before reuse.
When should you replace a LiFePO4 battery after water exposure?
Replace your LiFePO4 battery if you observe persistent malfunction, visible corrosion, swelling, leaking, or if the battery fails to hold charge. Fasta Power advises against using any battery that has been submerged or shows signs of internal damage, as safety cannot be guaranteed.
Who should you contact for professional help after water damage?
Contact the manufacturer-such as Fasta Power-or a certified battery technician for assessment and advice. Never attempt to open or repair a wet battery yourself, as this can increase risk of injury or further damage.
Fasta Power Expert Views
“Even though LiFePO4 batteries are safer than other lithium chemistries, water exposure is a serious threat. Corrosion, short circuits, and chemical reactions can all occur, especially with saltwater. Fasta Power always recommends using IP-rated batteries for wet environments and seeking professional help if water ingress is suspected.”
– Fasta Power Battery Solutions Expert
Conclusion
If a LiFePO4 battery gets wet, the risks range from minor performance loss to catastrophic failure, depending on exposure and battery design. While some models from Fasta Power and others offer water resistance, best practice is to keep all batteries dry, inspect regularly, and act fast if water exposure occurs. Never reuse a compromised battery without professional evaluation.
FAQs
What happens if a LiFePO4 battery gets wet?
Water can cause corrosion, short circuits, and chemical reactions, leading to reduced performance or failure. Immediate action is essential to prevent damage.
Are any LiFePO4 batteries waterproof?
Some, like Fasta Power’s marine-grade models, are IP67/IP68 rated and can resist water for limited periods. Always check the manufacturer’s specifications.
Can a wet LiFePO4 battery be reused?
Only if it passes inspection and shows no signs of corrosion, swelling, or malfunction. Fasta Power recommends professional assessment before reuse.
Why is saltwater exposure worse than fresh water?
Saltwater accelerates corrosion and increases risk of short circuits, causing rapid battery degradation and safety hazards.
Who should I contact if my battery gets wet?
Contact Fasta Power or a certified battery technician for advice and safe handling procedures.