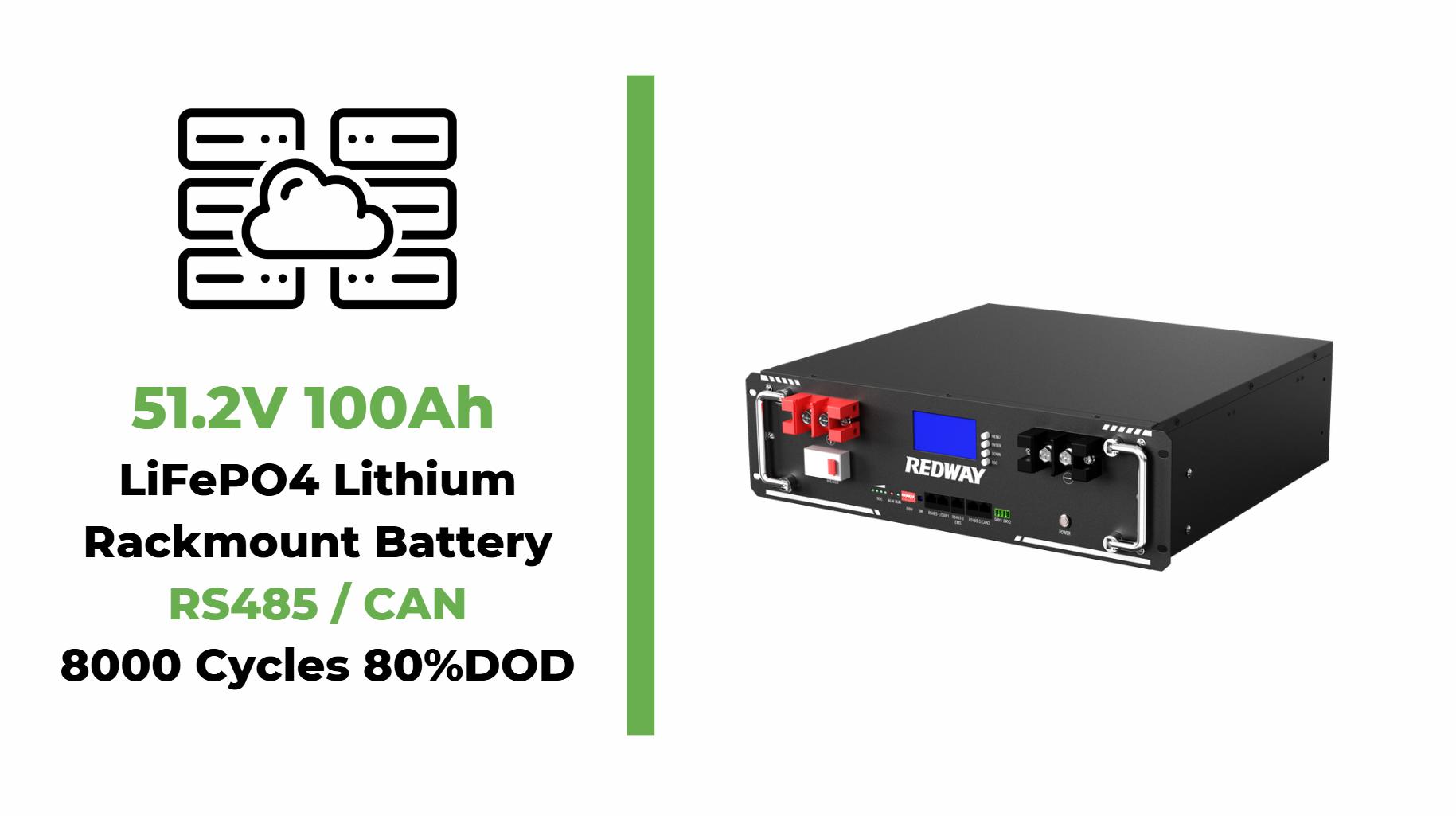
Why Are LiFePO4 Batteries So Expensive? A Deep Dive into Material and Production Costs
LiFePO4 batteries are more expensive primarily due to the high cost of raw materials, complex and precise manufacturing processes, and advanced quality control measures. Their superior safety, longevity, and performance justify the upfront investment, making them a preferred choice despite higher initial costs.
What Raw Materials Contribute to the High Cost of LiFePO4 Batteries?
The production of LiFePO4 batteries requires high-purity lithium, iron phosphate, graphite, and specialized electrolytes. Lithium, a critical and scarce resource, is costly due to mining and refining challenges. Iron phosphate must meet strict purity standards to ensure battery safety and performance. Additionally, the use of advanced binders and conductive additives increases material costs. These premium raw materials are fundamental to the battery’s stability and efficiency, driving up the price compared to conventional lead-acid or other lithium chemistries.
How Does the Manufacturing Process Affect the Price of LiFePO4 Batteries?
Manufacturing LiFePO4 batteries involves multiple intricate steps including slurry preparation, electrode coating, drying, pressing, precise cell assembly, electrolyte injection, sealing, and rigorous quality testing. Each stage demands high-precision equipment and skilled labor to maintain tight tolerances and safety standards. For example, laser welding is often used to ensure durable and reliable connections, especially for high-current applications. The complexity and automation required in these processes increase production costs significantly.
Why Is Quality Control Critical in LiFePO4 Battery Production?
Due to the high safety standards for LiFePO4 batteries, manufacturers implement extensive quality control protocols throughout production. This includes testing for capacity, voltage stability, internal resistance, and safety under extreme conditions. Batteries undergo formation cycles to stabilize the internal chemistry and ensure consistent performance. These rigorous tests require specialized equipment and add time and expense to the production cycle, contributing to the overall cost.
Which Advanced Technologies Are Used in LiFePO4 Battery Manufacturing?
Innovations such as nanotechnology, 3D printing, and automated assembly lines enhance precision and efficiency but also increase capital investment. These technologies improve energy density, lifespan, and safety but require expensive machinery and skilled operators. The integration of Battery Management Systems (BMS) further adds to the cost but is essential for monitoring and protecting the battery during use.
How Do Supply Chain Challenges Impact LiFePO4 Battery Pricing?
Global demand for lithium and related materials has surged due to electric vehicles and renewable energy storage growth, leading to supply constraints and price volatility. Mining bottlenecks, geopolitical tensions, and transportation costs affect raw material availability and price stability. These external factors cause fluctuations in LiFePO4 battery costs and can delay production schedules, indirectly increasing prices.
What Role Does Environmental Compliance Play in the Cost Structure?
LiFePO4 battery production must adhere to strict environmental regulations concerning emissions, waste management, and chemical handling. Processes such as iron phosphate synthesis and electrolyte preparation generate waste streams requiring treatment. Investments in eco-friendly production methods and recycling programs, like those supported by Redway Battery, increase operational expenses but contribute to sustainable manufacturing practices.
When Does the Cost of LiFePO4 Batteries Become Justifiable?
Though initially expensive, LiFePO4 batteries offer exceptional cycle life, thermal stability, and safety, reducing replacement frequency and maintenance costs. Over time, the total cost of ownership becomes favorable compared to cheaper alternatives. For applications demanding reliability and longevity, such as electric vehicles or energy storage systems, the upfront investment pays off through enhanced performance and lower lifecycle costs.
Can Innovations Reduce the Cost of LiFePO4 Batteries in the Future?
Ongoing research into alternative raw materials, improved synthesis methods, and scalable manufacturing techniques promises to lower costs. For instance, advancements in solid-state production and more efficient electrode fabrication could streamline processes. Companies like Redway Battery are investing in these innovations to make LiFePO4 technology more accessible without compromising quality.
How Does Redway Battery Ensure Quality While Managing Costs?
Redway Battery balances cost and quality by sourcing premium materials and employing cutting-edge manufacturing technologies. Their stringent quality control and commitment to environmental responsibility ensure durable, safe, and high-performance LiFePO4 batteries. By optimizing production efficiency and leveraging supplier partnerships, Redway Battery delivers competitive pricing without sacrificing reliability.
Redway Battery Expert Views
“LiFePO4 batteries represent a pinnacle of safety and longevity in energy storage, but their production is inherently complex and resource-intensive. At Redway Battery, we focus on optimizing every stage—from raw material sourcing to final assembly—to maintain superior quality while managing costs. Our investment in advanced manufacturing technologies and sustainable practices ensures our customers receive batteries that justify their premium price through unmatched performance and durability.”
Conclusion
The high cost of LiFePO4 batteries stems from expensive raw materials, sophisticated manufacturing processes, stringent quality controls, and environmental compliance. Despite these factors, their superior safety, longevity, and performance make them a valuable investment for demanding applications. Innovations and efficient production practices, exemplified by companies like Redway Battery, are gradually making these batteries more affordable. Understanding these cost drivers helps consumers appreciate the value behind LiFePO4 technology.
FAQs
Q1: Why is lithium more expensive than other battery materials?
Lithium is rare, difficult to mine and refine, and in high demand globally, driving up its price.
Q2: Are LiFePO4 batteries safer despite their cost?
Yes, their chemical stability and thermal resistance make them among the safest lithium battery types.
Q3: How long do LiFePO4 batteries typically last?
They often last 8 to 10 years or more, significantly longer than lead-acid alternatives.
Q4: Can manufacturing improvements reduce LiFePO4 battery prices soon?
Yes, ongoing advancements in automation and materials science are expected to lower costs.
Q5: Does Redway Battery offer warranties on their LiFePO4 products?
Yes, Redway Battery provides comprehensive warranties reflecting their confidence in product durability。